The Creation Process
Copper Wheel Engraving is an old-established technique of cutting and engraving glass, having been established in Germany and Holland in the 15th and 16th centuries, and enjoying an unbroken tradition since then. Copper-Wheel engraving is considered one of the most difficult art forms known to man as the craft takes 10 years to master.
The glass is cut with a copper wheel or disk, rotated in a lathe, whose edge is charged with an abrasive powder suspended in oil. The wheel is fixed, and the glass is offered up to the wheel to make the cut. By using different rotational speeds, different size and edge profile of the wheel, and types of abrasive, a wide variety of texture and line effects may be achieved. Larger wheels with a rounded or vee-shaped profile may be used to give deep cutting which is difficult to achieve with flexible drive engraving. On the other hand, free-hand and calligraphic work are more difficult with the copper wheel.
The copper wheel can be used with softer abrasives such as iron oxide (rouge) or zirconium or cerium oxides, to polish and soften the texture of glass engraved with other techniques. Look very closely at the incredible detail from the smallest bud vase to the largest trophy. Every piece is hand-held to one of 50 spinning copper-wheels as each stroke of the design is engraved into the crystal by hand. Nothing, but absolute perfection in every cut.
Through the ages, artists have delighted in seizing the moods of life, of nature and of precious moments, fixing them in time for all of us to enjoy. Crystal is the perfect medium for the elegant beauty of engraving and these Ancient arts have been practised by man for thousands of years. The artist is able to express himself with the most delicate of strokes of the copper wheel on crystal.
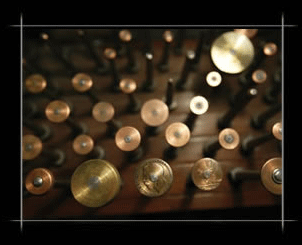
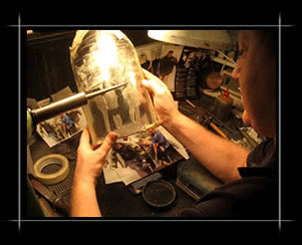